In this article, you will learn how to predict linear and exponent coefficients for a power law porous media modeling using experimental data.
Overview
In our simulations, often times we have to model a structure as a porous media. These structures can be as simple as perforated plates and as complex as radiators. The objective, however, is the same: save mesh cells while still accounting for local pressure losses.
In the Power Law formulation, pressure losses are given by:
where:
is the pressure drop across the porous media ; is the density of the fluid ; is the thickness of the porous zone ; is the fluid velocity ; is the linear coefficient and; is the exponent coefficient.
With the power law formulation, pressure drop will always be isotropic within the medium. If your media is anisotropic, make sure to check out the Darcy-Forchheimer approach. For compressible flows, check the Fixed Coefficient model.
Power Curve Fitting Approach
Using experimental data for pressure versus velocity, we can extract the coefficients.
For example, let’s take a 0.01 meters thick perforated plate and water as fluid. The following case was simulated in SimScale at 6 different velocities.
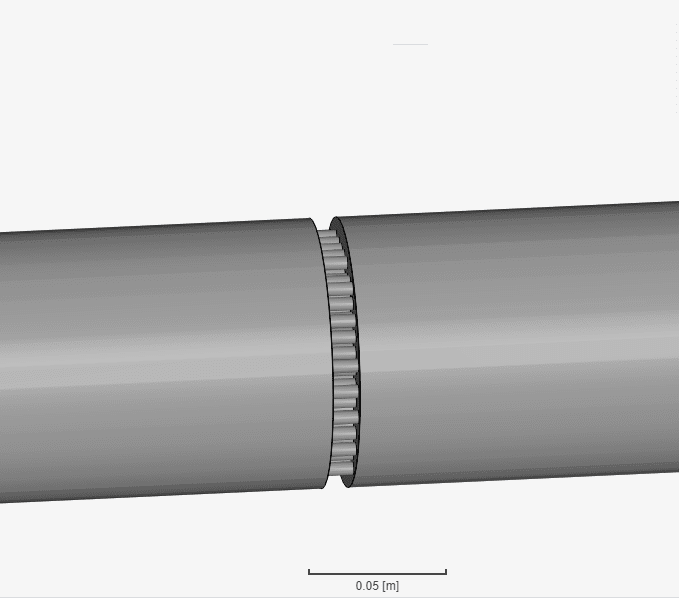
Instead of simulating the original geometry of the perforated plate, we will model it as a porous medium. In the platform, you can readily create a porous media and assign it to a volume or a geometry primitive such as the cartesian box shown below:
The table below shows the results from the simulations:
Velocity | Pressure drop |
0.5 | 960 |
0.7 | 1840 |
1 | 3720 |
1.2 | 5390 |
1.5 | 8240 |
2 | 14690 |
By fitting this data set with a power curve, we get the following:

The expression below is extracted from the plot:
From that, we obtain
Now to compare experimental data with simulation results:
Thus, the power law model proves to be accurate in accounting for pressure losses.
Note
If none of the above suggestions did solve your problem, then please post the issue on our forum or contact us.