In the initial design stages of components for industrial machinery, finite element analysis (FEA) is often used to look for ways in which performance and durability can be improved. When assessing a model’s performance, many forms of mechanical behavior that need to be analyzed are rate-dependent, meaning that a model cannot be simply tested in its current state. Instead, the material’s response to certain loading conditions should be analyzed at different steps over the course of the simulation.
For example, you might ask, “how will this product perform when exposed to temperature or pressure changes?”. If a product is exposed to extremely high temperatures, the chances of cracking, buckling or breaking apart increase which could lead to disastrous outcomes. This comes down to material properties, and testing these properties through FEA structural analysis.
Linear or Non-Linear Materials in FEA: What’s the Difference?
When we talk about linear and non-linear materials we are primarily referring to the relationship between stress and strain in the material. If the stress remains proportional to the strain, the material properties are considered to be linear and it behaves elastically, otherwise, the mechanical properties are considered to be non-linear. Material non-linearity requires a non-linear simulation approach, as forementioned, through FEA structural analysis.
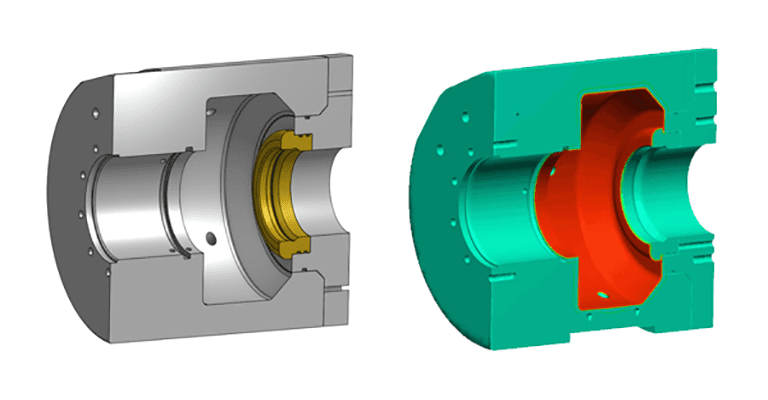
A non-linear simulation is one in which the stiffness matrix of a structure changes during the course of the run. Material property changes affect the stiffness matrix of the structure, and non-linear stress-strain relationships are a typical cause of changes in material properties during the course of a simulation. On this note, we want to look at transient simulations in which material properties change over time due to, for example, temperature dependence. Like material property changes, large deformations can also alter the stiffness matrix, as the structure and reference frames of the model are shifted. The same goes for physical contacts, where load and stress are transferred between two parts that come into contact, thereby changing the stiffness of both. It is this lack of direct proportionality between stress and strain of a material which leads it to be described as non-linear.
Our Case: Combustion Chamber
To demonstrate structural analysis using non-linear, temperature-dependent materials, SimScale used a combustion chamber provided by Explotechnik AG. The combustion chamber consists of a brass rim (which possesses linear elastic material properties) combined with a main body made of S355 steel, which exhibits temperature-dependent plastic behavior. The combustion chamber, and all materials used in its assembly, must be able to withstand extremely high temperatures and so it was the ideal test subject for non-linear structural analysis.
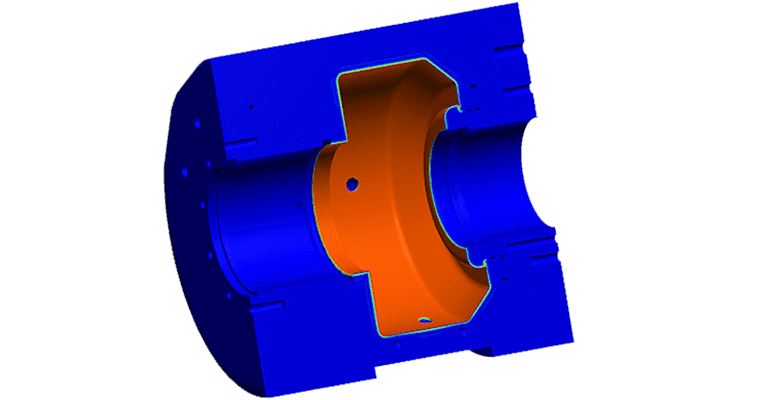
In addition to the model, Explotechnik provided multiple bi-linear stress-strain curves for the nonlinear steel at different temperatures. The table upload feature from SimScale allowed all the material information to be uploaded quickly. Solvers in the workbench also linearly interpolated the stress-strain curves between the temperatures provided. Using this information, the simulation was set up to see how temperature, pressure, and mechanical stresses evolved over time and how these affected the non-linear steel.
Simulation Workflow
The CAD model was imported and automatically meshed to save time, with 314 nodes in just five minutes. With SimScale FEA, contacts between surfaces in multi-body models can be automatically detected. In this simulation, the bonded contact between the end piece and the main body was detected, as well as a bond between the brass piece and the rest of the model. A topological set of all “application surfaces” was set up so that temperatures and stresses could be applied to the relevant parts of the model in one, rather than needing to select each surface individually, thus further speeding up the process.
For this thermomechanical simulation, heat transfer was enabled on the bonded contacts and the thermal load was set as transient. A heat transfer coefficient was used in order to see temperature response on the application surfaces (rather than the temperatures remaining fixed at the inputted values). And finally, a plastic material behavior was applied to the steel to reflect its nonlinearity.
Results
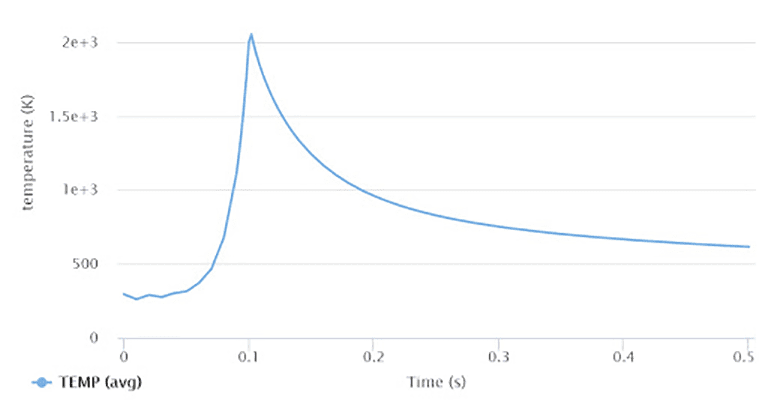
The main results to consider are the average temperatures on the application surfaces and principal stress. The finite elements on the application surfaces became subject to high levels of compression during combustion, however only at surface level. This suggests that it should not present too much of a concern for performance in the short term, however, from a perspective of fatigue analysis, the designer might consider making improvements to avoid deformations occurring in the long term. Looking at the temperature response of the materials, there is a difference in temperature load which reduces slowly after combustion has occurred.
The results demonstrate how mechanical stresses are concentrated on the brass rim, induced by thermal shock. Stress is also concentrated on the exposed edges of the internal combustion chamber, a potential pain point as crack propagation could occur.
Conclusion
In models using temperature-dependent materials, it is crucial to assess how they will perform when exposed to thermal shock and after thermal shock has occurred. As can be seen from our subject of a combustion chamber, FEA structural analysis shows how materials, such as non-linear steel, perform under thermal and pressure loading. It can also reveal weaknesses in the structural makeup of a design which are likely to affect the lifespan of the model. From the results of a structural analysis, a design engineer can make a more informed performance prediction of the component or product being simulated and improve the design accordingly.