Turbomachinery design demands innovative methods to explore vast design spaces with high precision. Traditional design and simulation approaches, relying on proprietary correlations and simplified models, often fail to provide the accuracy needed to minimize the need for large safety margins and optimize designs effectively and efficiently. The challenge intensifies with harmonizing simulation results for new designs where no test data is available. These limitations can lead to suboptimal designs, increased costs, and longer development cycles.
A cloud-native simulation platform like SimScale addresses these challenges by offering scalable, cloud-based computational resources. This enables detailed and extensive simulations without the constraints of local hardware. Such scalability accelerates the design process and fosters enterprise-wide collaboration, allowing engineers, designers, and simulation experts to work together seamlessly across different locations. As a result, not only is the simulation cycle time shortened, but the simulation lead time from the moment the designer requests a simulation to when the simulation starts is also considerably minimized.
Integrating artificial intelligence (AI) into cloud-native simulation further enhances these capabilities. AI optimizes complex workflows and identifies patterns and correlations so quickly that it significantly improves the accuracy and efficiency of simulations. By leveraging AI, engineers can uncover deeper insights, set more precise predictions, and make more informed decisions. At SimScale, and in collaboration with NAVASTO, we integrate AI with our cloud-native PDE solvers to provide engineers with an enhanced toolset for creating robust and comprehensive turbomachinery designs. This combination empowers engineers to tackle a wider design space with greater confidence and speed, driving innovation and efficiency in the field.
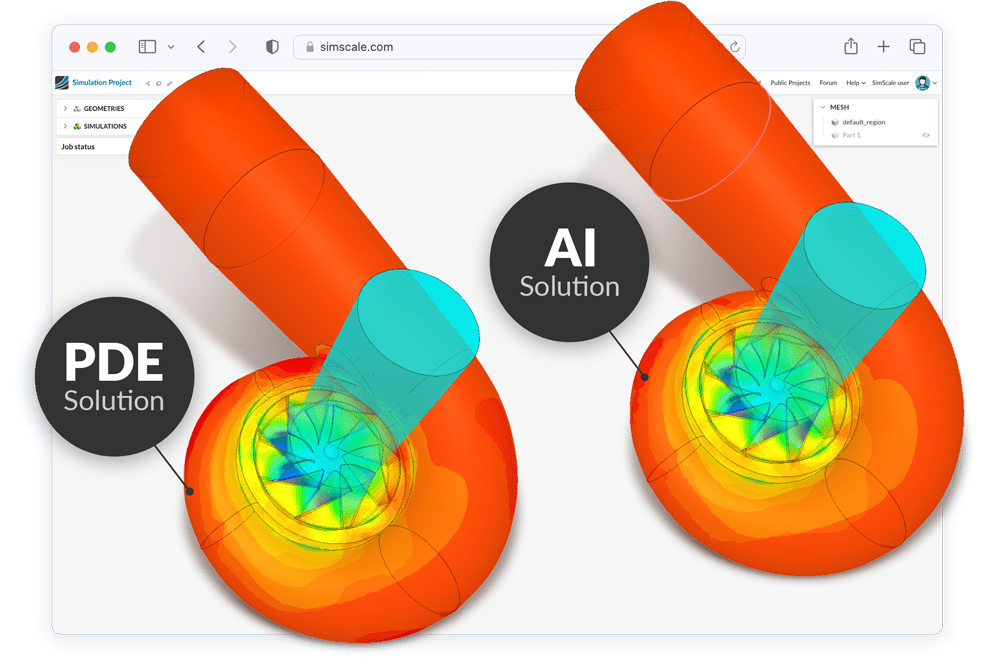
The Classical Design Approach to Turbomachinery
When designing industrial turbomachinery, designers and engineers typically depend on empirical methods and cumulative experience building turbomachines for specific applications.
- The classical design approach can be summarized into four distinct steps:
- Design space definition (based on desired duty point and geometric and kinematic constraints)
- Stage design (i.e., designing the blades and directly analyzing and iterating until the design converges on the duty point)
- Numerical verification (CFD simulation to verify the results of the stage design step)
- Experimental testing
In such a traditional approach, designers can minimize the uncertainty in their predictions only during their verification step, making use of differential methods such as computational fluid dynamics (CFD), structural mechanic analysis, and sometimes even multi-objective optimization algorithms. Typically, these methods depend on simplified models due to computational constraints brought about by on-premise simulation software and the corresponding local hardware, especially when running thousands of iterations. One example of such methods is RANS vs LES or DNS for aeromechanic applications. However, with the advent of Industry 4.0 and the integration of digital solutions to optimize products and exchange data in manufacturing technologies, things have begun to change, and, as researchers have noticed, “The turbomachinery community is witnessing a great push in rethinking all manufacturing activities.”
Cloud-Native Simulation for Industrial Machinery Manufacturing
Our latest eBook explores how cloud-native simulation is transforming challenges of industrial machinery manufacturing (including turbomachinery) into opportunities. Download it for free by clicking the button below.
Introducing AI and Cloud-Native Simulation to Turbomachinery Design
Cloud-native simulation has introduced a complete revamp of the classical design approach, enabling simulation to be used beyond the limited verification step. With its relatively unlimited computing power and freedom from any local hardware or software constraints, the use of a user-friendly, cloud-native simulation platform like SimScale can be democratized and deployed across the whole design process and all stakeholders in the company. Now, designers can use simulation early in the design cycle, enabling them to run as many iterations as needed simultaneously — which is not achievable with traditional simulation tools — get faster results, and make informed decisions more quickly.
The large, heterogeneous data sets of turbomachinery design, characterized by varying levels of resolution, accuracy, availability, and operating conditions, establish significant challenges to design and engineering teams trying to conciliate such data sets into a design system. Cloud-native simulation helps overcome these challenges by leveraging cloud computing and its ease of data exchange. Meanwhile, data-driven design methods like machine learning (ML) — a discipline of AI — can benefit significantly from large volumes of data, drawing upon algorithms to find patterns and structure within these data sets.
As a result, AI can assist cloud-native simulation in generating almost instantaneous simulation results based on continually-improved, data-driven predictions. By analyzing historical data from numerous simulations and real-world performance metrics, these algorithms can identify patterns and make informed predictions about future performance. This continuous learning process allows for more precise simulations, reducing the need for extensive trial and error and enabling engineers and designers to focus on innovation and optimization.
Today, a cloud-native simulation infrastructure is the only way to leverage AI to its full potential, as all simulations are readily available for AI training on cloud GPUs.
In fact, turbomachinery simulation projects can benefit from AI in accelerating the execution of complex simulations or, soon enough, filling the gaps in CAE models using generative AI. Today, a cloud-native simulation infrastructure is the only way to leverage AI to its full potential, as all simulations are readily available for AI training on cloud GPUs. With the addition of new data, retraining AI models becomes a relatively simple process. On SimScale, AI CAE models are run alongside CFD simulations in the same workbench, utilizing AI results for rapid assessments and CFD for validation purposes.
Scalability and Accessibility with Cloud-Native Simulation
The integration of AI with cloud-native simulation on SimScale, powered by NAVASTO, amplifies the benefits mentioned before by leveraging virtually unlimited computational resources. This scalability is crucial for handling the large-scale, complex turbomachinery simulations. Engineers can run multiple simulations in parallel, exploring a wide range of design parameters and scenarios without being constrained by local hardware limitations.
Engineers can also access SimScale from any device with internet connectivity anywhere in the world, facilitating real-time collaboration and knowledge sharing. This global access democratizes simulation, allowing teams to leverage diverse expertise and drive innovation collectively.
Driving Innovation with AI-Enhanced Insights
One of AI’s most significant advantages in simulation is its ability to uncover insights that traditional methods might miss. By processing and analyzing large volumes of data, AI can identify subtle trends and correlations that inform better design decisions. For instance, AI can predict how minor changes in the geometry of a pump or material properties of a compressor blade will impact overall performance without running the full simulation, thereby enabling engineers to optimize designs with a higher degree of precision.
Moreover, AI-driven simulations can incorporate multiple-physics interactions, capturing the complex interplay between various physical phenomena such as fluid dynamics, heat transfer, and structural mechanics. This holistic approach provides a more comprehensive understanding of system behavior, leading to more robust and efficient turbomachinery design.
On-Demand Webinar
Interested to learn more about SimScale’s multiphysics simulation capabilities? Watch our dedicated on-demand webinar.
Empowering Engineers with AI-Driven Tools
Ultimately, the goal of integrating AI with cloud-native simulation is to empower engineers. AI-driven tools do not replace the need for human expertise; instead, they augment it by helping to channel heavy-duty simulations over a narrower design space. By automating routine tasks and providing deeper insights, these tools free up engineers to focus on creative problem-solving and strategic decision-making.
For instance, AI can handle the heavy lifting of data analysis, allowing engineers to concentrate on interpreting results and exploring innovative solutions. This symbiotic relationship between human intelligence and AI-driven capabilities leads to more efficient workflows, better designs, and faster time-to-market.
SimScale’s vision for AI in turbomachinery simulation is expansive and forward-looking. We believe that AI will continue to push the boundaries of what is possible, enabling engineers to tackle increasingly complex challenges with confidence and precision. Our commitment to integrating AI with cloud-native simulation is driven by a desire to empower engineers to innovate faster and drive continuous improvement across the industry.
In the future, we envision AI playing an even more integral role in simulation, from automated optimization routines to advanced machine learning models that can predict performance with unprecedented accuracy. As AI technology continues to evolve, so too will its applications in turbomachinery design, leading to smarter, more efficient, and more reliable machinery.