Electrical engineers and PC hobbyists alike know the critical value of a CPU cooling system. Without them, sensitive electronic components face a negative impact on performance or, at worse, permanent physical damage. As more and more computing power is expected from our devices, so too grows the need for effective electronics cooling.
Cloud-based simulation equips engineers with the ability to test multiple scenarios and validate designs without the time-consuming and costly practice of prototyping for each iteration. This article shows you how and presents a case study from Forwiz System, who used thermal simulation to further optimize a CPU cooling system, winning their client improved product performance at less cost.
What is a CPU Cooling System?
A CPU cooling system effectively moves heat away from sensitive (and expensive) component parts through the use of heat pipes and heat sinks. Heat pipes are rapid heat-transferring devices with high thermal conductivity, sometimes up to 100 times more effective at conducting heat than typical metals.
Heat pipes transfer heat generated by the CPU towards the heat sink. The functionality of the heat sink is to increase the contact area with air to accelerate the final dissipation of heat via natural or forced convection to the surrounding environment. For the effective performance of the CPU cooling, each component needs to be optimized.
How to Improve CPU Cooling with Simulation
By nature, the design process for electronics cooling is very iterative. CPU cooling systems entail many parameters, and each plays a critical role. In their journey towards optimization, engineers are presented with a variety of strategies to experiment with including adjusting the number of heat pipes or changing their diameter, increasing the number of heat sink fins or adjusting their thicknesses, use of surface treatment, radiative paint for optimal heat loss via thermal radiation or testing out different materials.
As engineers are striving for the optimal solution across these multiple parameters, virtual testing before prototyping represents a huge cost and time-saving opportunity. A traditional design workflow for a CPU cooling system involves testing designs against their expected results, often a target temperature.
Electronics design that does not achieve the required cooling performance during thermal analysis requires a second or third iteration which means manufacturing more than one prototype. Manufacturing, shipping, and prepping the prototype for testing all contribute to time delays and increase the number of steps in the process, and thus, the number of possibilities for issues. With simulation, engineers have access to testing many scenarios in a simpler workflow with shorter turnaround times. A design tested and optimized for simulation can then be moved along to the final stage of the process, i.e., prototype testing, and the cost and time investment associated with it need only occur once.
Cloud-based simulation takes this even further. With computing power off-loaded to servers, high-fidelity engineering simulation is made accessible, regardless of an engineer’s hardware capacity. Cloud-based simulation platforms, like SimScale, make it possible to run all simulations in parallel, driving down the design process from weeks to hours. Rapid iterations in-house eliminate the need for external simulation consultants, which provides cost savings, as EUROpack A/S. found when integrating SimScale into their workflow.
Case Study: Forwiz System
Forwiz System, an IT services company, received a request from a client to improve the cooling of the CPU inside their 2U servers. The cooling needs of their CPU chip, which had many cores, were not being met by the CPU coolers readily available on the market. In fact, when the chips were fully operational the CPU temperature was easily exceeding 90 degrees Celsius. This restricted their CPU from being fully operational.
As the position and arrangement of different components installed inside their server were fixed, Forwiz had to work within the existing system to take on the challenge.
To achieve better cooling performance they first increased the width of the upper part of the heat sink, taking advantage of previously unused, surrounding space. Then, they added more heat pipes to the newly increased size and lastly, they applied a special paint that has high-emissivity for additional thermal radiation.
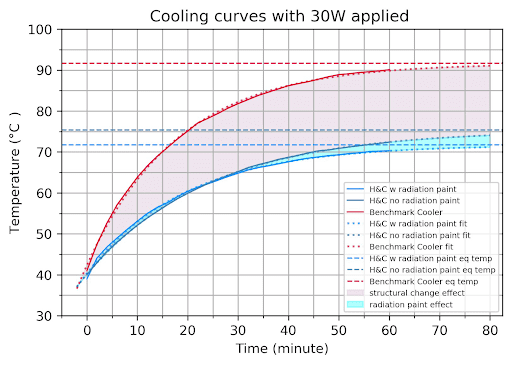
Results from their initial experiment show that the structural change significantly increased performance when compared to the existing “benchmark” cooler design. The effect of the radiation paint also contributed to a drop in temperature, but not significantly which is important to note because that requires extra cost and manufacturing process.
The changes to the CPU cooling system made by Forwiz dropped the operating temperature from 90 degrees C down to 80 degrees C, within five degrees from the target temperature at which the client’s CPU chips could be fully operational. With cloud-based simulation, the engineering team was able to further optimize and deliver the target temperature for their client.
Forwiz used SimScale’s CHT solver to test the geometry of heat pipes and the number of fins within the CPU cooler and to validate the effectiveness of their previous cooling strategies.
With more than 100 simulations run, the results not only showed that their original structural changes contributed to a 15-degree C decrease in temperature but revealed that the high-emissivity paint could account for another 4 degrees C. The new heat sink geometry, optimized via simulation, reduced the temperature by another 5 degrees C. With the newly proposed CPU cooling system, the final temperature reached was around 77-76 degrees C, achieving the target temperature set by their client.
For Forwiz, simulation enabled the engineering team to reach optimal cooling performance and facilitate the full operating capacity of their client’s CPUs. Simulation in the cloud is a powerful tool for designers seeking optimal thermal management in a quick and highly iterative manner.
To learn more about electronics cooling and how engineers can optimize the thermal management of their designs with SimScale, check out more resources here:
- The Evolution of Evaluating Thermal Management: SimScale Customer Spotlight
- Thermal Management: Lighting, Battery, and Enclosure Cooling Projects
- Conjugate Heat Transfer Simulation: Best Practices in SimScale