As components, parts, devices, and products are expected to last longer, perform better, be updated faster, and cost less, engineers are faced with increasingly complex design challenges that were unimaginable only a decade ago. Adopting a modern workflow in the product development cycle liberates designers and engineers from legacy software constraints and hardware limitations resulting in less physical prototyping.
In this blog article, we discuss a centrifugal pump use case where engineers are faced with the challenge of optimizing the pump design based on seven parametric variables. A fully integrated and automated workflow is used, linking three cloud-based CAE solutions: Onshape, SimScale, and the engineering tools offered by ESTECO.
Onshape: Cloud-Native CAD
The simulation workflow starts with a mechanical CAD model of the centrifugal pump, which is designed in Onshape. Onshape offers a cloud-native product development solution that enables designers and engineers to access their design documents and collaborate from anywhere, on any device.
The model has seven key geometric parts to it that have been parameterized, allowing for design variations that can be automated. These include the blade angle, thickness, radius, number of blades, inlet length, and diffuser dimensions.
Each variation in the above parameters gives a new CAD model generated in Onshape. Using the APIs, these CAD variants are pushed from Onshape to SimScale, for simulation and analysis.
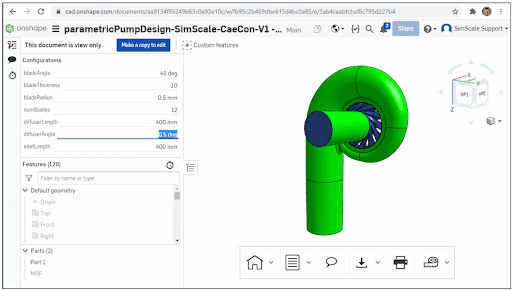
ESTECO: Multidisciplinary Design Optimization
The centrifugal pump CAD model has seven geometric design parameters. Engineers might want to evaluate 10 values per parameter, to begin with, giving up to 1 million possible design variants that would need testing. This represents an extremely large solution space that would be time and cost-prohibitive to explore. A method is needed to downsize the number of potential final design values without compromising on optimum efficiency.
Using the integrated workflow between Onshape, SimScale, and the optimization tools offered by ESTECO, the 1 million design permutations are reduced to only 65, using Multidisciplinary Design Optimization (MDO) available in modeFRONTIER (from ESTECO).
This optimization technology is game-changing for two reasons: The design update process is fully automated, and the optimization is driven by a highly efficient self-adaptive algorithm capable of searching for the global optimum within the solution domain, using a very limited number of design iterations and therefore bypassing the classical trial-and-error approach. This objective-driven optimization step intelligently chooses which parameters to change and optimizes the design for maximum efficiency, as defined by the engineer.
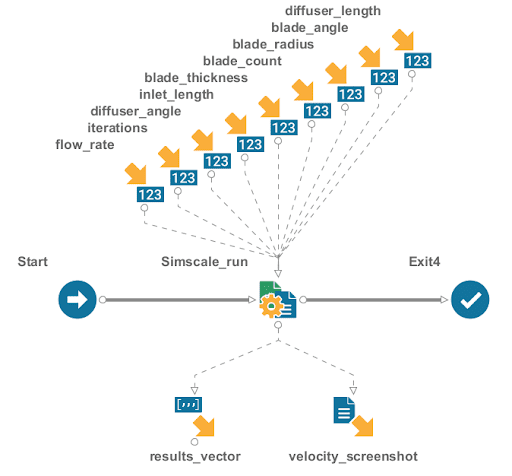
SimScale: Cloud-Native CFD Simulation
The SimScale platform provides an API layer that allows access to all of the different physics and simulation capabilities in addition to geometric parameters. In this case, SimScale is used to perform an incompressible CFD analysis on each of the 65 CAD geometry variants.
All 65 CAD models are simulated in parallel using a single simulation setup for meshing, boundary conditions, material properties, and solver parameters. SimScale will output results for physical variables such as total head, pressure drop, flow velocity, temperature, etc., that can be used to calculate pump efficiency and feed into the optimization algorithms.
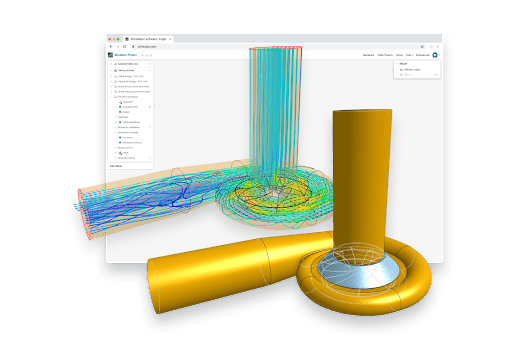
Modeling, Simulation, and Optimization with Cloud-Native Software Stacks
Once the simulations are complete, engineers can receive notifications and begin to analyze the results in SimScale or third-party tools. In this example, the simulation process workflow, together with the defined optimization strategy, is then uploaded to the VOLTA platform to execute the runs in a distributed environment.
Optimization results are then post-processed in the VOLTA Advisor tool, using advanced visualization tools to address the optimized centrifugal pump design directly in the browser. Results can be easily shared with members of the project team. This workflow also includes a feedback loop. Using ESTECO’s tools, engineers can then select which parameters to alter during run-time in order to continuously optimize the design further.
By adopting a modern cloud-native CAD and simulation tool workflow together with process automation and decision optimization stacks, organizations can implement a design-simulate-optimize workflow in their product development cycle.
Whitepaper: Engineering Design, Simulation, and Shape Optimization
To learn more about the power and value of geometric parameterization of a simulation model coupled with design optimization feedback, download our whitepaper: