This article is the first in a series of three about discovering the benefits of cloud-based FEA simulation using finite element analysis (FEA) in general and SimScale in particular, as the structural analysis software.
I have been using the finite element method (FEM) and structural analysis software since engineering school. It all started with research projects for the industry. I was the assistant in charge of setting up and running the simulations, writing and debugging the code, analyzing the results and writing the reports. During that time, I not only learned the theory behind FEA, but I also gained a deep insight into the implementation and practicality of the technique. Throughout this time, I had the opportunity to solve real-world problems using many different tools, ranging from custom solvers written from scratch to the most famous, fully-featured commercial solutions.
One of my main concerns was the cost of carrying out the simulations with an on-premises structural analysis software. Many vital activities including meshing, solving and post-processing the results required workstations with large amounts of memory and fast processors to be practical. Even with a top-of-the-line computer at that time, a structural simulation with around half a million degrees of freedom could take several hours to run, if not one to two days. I clearly recall leaving the simulation running on Friday only to arrive early on Monday and discover that something went wrong or the simulation didn’t converge. This meant I had to start all over again, and the entire process was delayed by another couple of days. Failure modes ranged from interrupted power to memory exhausting or numerical errors.
At that time, we had many conversations about parallelization and clusters of computers to improve our simulation capabilities. Attempts were made, but successfully setting up such a system proved to be a challenge. The closest we got was the acquisition of a server with 32 cores and 96 gigs of RAM. Still, I think we never realized the maximum potential of engineering simulation, mostly because of lack of proper software.
Cloud-Based Structural Analysis Software
Fast forward to 2017: we now have technology on our side, which can help overcome many of these limitations. From the first time I heard of cloud computing and big server farms, I was intrigued and started exploring their application to simulation. I knew that within many companies and agencies there were server farms working on FEM and CFD simulations, but not many of them were available to the public, and none were easy to use or could be paid for. That is why finding SimScale was a happy discovery for me (and surely for many other simulation engineers).
I can now tackle projects with my consultancy company that were previously impractical or very lengthy (thus expensive) to implement. I had never thought of running simulations in the range of up to one to two million degrees of freedom, with the facility of setting them up from a web browser, shutting down my computer, and waiting for an email on my phone to confirm that the simulations had ended, so I could check the results. It was a game changer.
The first obvious benefit was that no hardware investment is needed. As a small consultancy company, buying and maintaining a high-end workstation proved financially challenging; firstly because of the long amortization period and secondly because of depreciation, as computers have the bad habit of failing after some time. Then imagine what it would mean to get access to a server farm that is fully functional and optimized to run simulation work. It was simply out of the question. With SimScale, I have instant access to supercomputer capabilities while only paying a fraction of the typical price of a traditional structural analysis software. And as a bonus, many of the problems of running lengthy simulations are gone: no more interrupted runs because of interrupted power, or finding out late that there was a numerical configuration error, or that it didn’t converge.
The Power of Cloud Simulation
Now I can, for example, run this propane tank burst analysis—a nonlinear plastic FEM simulation—with more than half a million degrees of freedom in about two hours and without worrying about memory usage, disk space for the results or long running times.
Here is another example: a Davit Crane, modeled with multiple bodies and contacts, discretized with around 1.6 million degrees of freedom, and run in under ten minutes. It is a linear static simulation, but it is amazing how one can make many iterations of the design, or explore alternative structural elements, all at an incredibly fast pace.
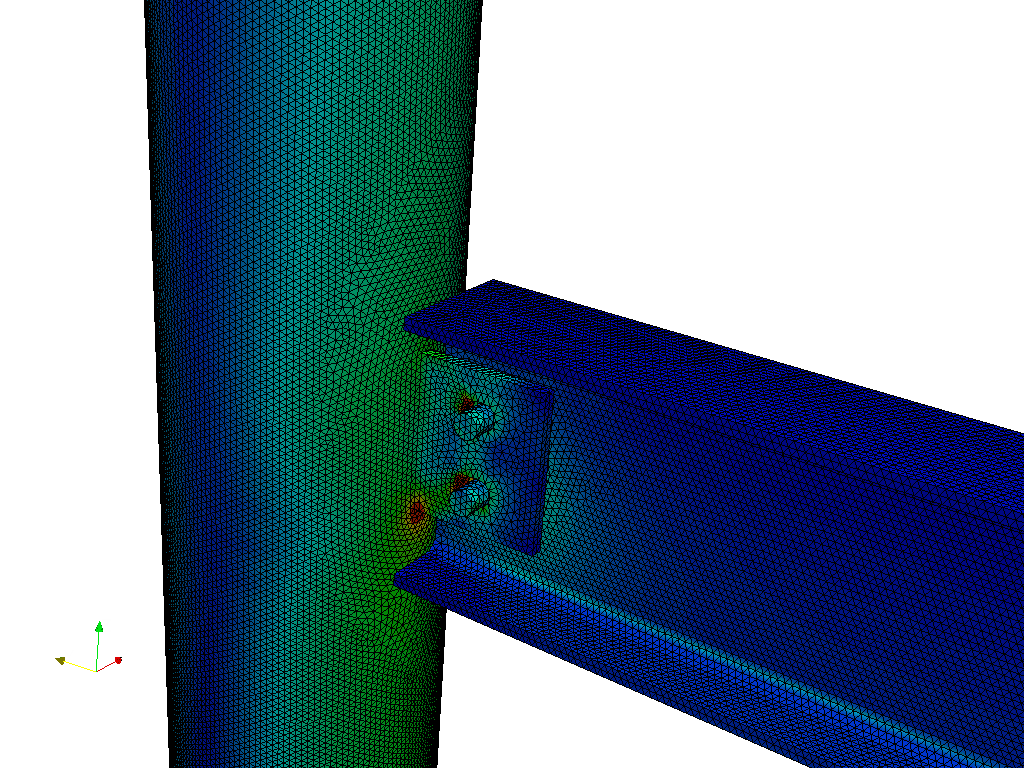
Both of these examples would require much more time to run if they were capable of being carried out on a desktop computer. This is the future of product design, and it’s already happening.
One can argue that these meshes of the CAD are overly refined and that simplified models could also work. But that is just transferring the work effort towards simplifying the model to overcome limitations that are not there anymore. The next step in computing power for structural analysis has this form, and also comes with a lot of additional benefits. Additionally, I believe that it brings us one step closer to definitive simulation solutions, such as Direct Numerical Simulation (and its equivalent in the structural simulation world), which I don’t think we will be able to run on a desktop computer.
I expect that by now you are convinced to give SimScale and the cloud simulation technology a chance. I am pretty confident that every FEM software user, from engineering students to researchers, professionals, and consultants can benefit from it. Go ahead, there is even a free trial to start with.
The purpose of a helmet is to protect the person who wears it from a head injury during impact. In this project, the impact of a human skull with and without a helmet was simulated with a nonlinear dynamic analysis. Download this case study for free.