I am working on Diffusers on our FSAE car. My simulation has run successfully but there is one problem. The pressure plotting in the post-processing is not good. I am getting constant pressure in the whole area. Including under my car, in front of the car, and behind the car which is of course completely wrong. Also, one of the wheels is also not rotating although I have given my wheels a rotating wall function.
I am attaching the link to my project:
Can any CFD expert help me regarding this issue? Thanks in advance!!
Tagging our experts @yosukegb4 & @dschroeder in this case to investigate what you could optimize.
Best,
Jousef
Hey @MihirRayganga
Here are some general things I noticed. Try out the following in the next simulation and see if this helps
- The reason one of your wheels isnt rotating is because you forgot to add a rotational velocity value. I have done this nuemerous times and i always try to double check my settings before simulating. It can be annying i know
-
Your bounding box is much too small for an FSAE car. Try a total of about 30 meters (10 in front 20 behind) Usually the bounding box should be 10x your geometry.
-
In your simulation control always turn on Potential Flow Initialization, it helps converge the solution quicker
-
Use the following for these values
- 0.06 for k
- 44.7 for w
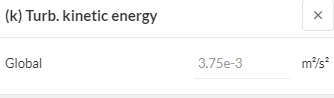

- some advice for your geometry
- meshes dont like sharp corners. the red arrows show where you should add fillets or chamfers to help avoid BL deletion. Also it would be better to increase the size of your contact patch for your tire
- Increase the size of your region refinement to include the whole car (red) and a slightly coarser cell region refinement behind the car for the wake.
Try this out and post again with your results
Dan
2 Likes
Hi everyone,
In addition to @dschroeder advices, “Tire F” rotates opposite direction in Run2.
Same as @dschroeder says , but please check your boundary conditions again.
Best,
Yosuke
1 Like
@dschroeder Thank you for these great insights. Do the incorrect values of k and w answer the incorrect pressure gradient around the flow region? And should these values be changed in every simulation?
Just another question, I have kept the maximum edge 0.01m for wake flow. Is it too high? what edge length should I keep (just a range would be fine) for the wake flow region and on the car?
Also, Thanks to @yosukegb4 for this little correction regarding values
I cant really say if the K and W values are the direct cause. They have more to do with how the flow is dispersed into the domain. These values can be exactly calculated but are dependent mainly on the domain size and your simulation setup. I have personally not gone very deep into these topics as i got these values from the Simscale FSAE Tutorial which had a domain size of :
(half car simulation)
length - 30m
width - 7m
height - 7m
So no you do not need to change these if you keep the same bounding box size.
0.01 should be a good size, its hard to say exactly how fine/coarse the wake box should be however doing refinements on large regions will increase the total cell count VERY quickly. If your simulations are taking too long or you have memory issues. This should be the first area to increase cell size.
The car region should have finer cells but as i said above it can quickly have a large impact on total cell count.
Best thing to do is to always start coarse and increase fineness where needed.
Dan
Sorry for the delay. I did corrections suggested by experts and also updated my geometry. The pressure problem was solved but I encountered a new problem - BAD RESIDUALS!
So here are my questions:
- My simulation didn’t complete and took a long time I don’t know why. Might be the refinements but I didn’t give very small refinements
- how can I fix my residuals because they are really bad and I can’t relly on this sim
Also, refer to the sim named 22-10 arc for this one
Thanks in advance
I suppose no one has yet looked upon this problem. Hence tagging @dschroeder @yosukegb4 to kindly guide me through the problem!!
Thanks in advance
Sorry for the delay. I did corrections suggested by experts and also updated my geometry. The pressure problem was solved but I encountered a new problem - BAD RESIDUALS!
So here are my questions:
My simulation didn’t complete and took a long time I don’t know why. Might be the refinements but I didn’t give very small refinements
how can I fix my residuals because they are really bad and I can’t relly on this sim
Also, refer to the sim named 22-10 arc for this one
Thanks in advance
Hey @MihirRayganga
Sorry i didnt respond. I did see this yesterday but i had a crazy day at work so i forgot to answer.
In your simulation, you have set the End time and Write interval to 1000. For a half car simulation, i would set this to 2000 minimum. A good test to do for your very first sim is to set these values even higher (5000) and watch the convergence plot. You will be able to see when the values stabalize and will then know where you should stop your simulations.
For example… if you see that after 1800 iterations the residuals become satable, then let it run for about 500 more iterations after that point and then use that as your new write interval for further simulations (2300)
This Message comes up when your Maximum runtime (from simulation control tab - see above) is exceeded. I would set this to a much higher number so that you wont get this message anymore (1.2e+5 or 4e+5)
Post again with your results
Dan
1 Like
Thank you Dan for the insight.
Talking about convergence, I have simulated Half car earlier and have got convergence in 1000 iterations. It has just started to happen recently that the simulation is not converging. What would be the reason behind this? bad geometry? or something else?
Also, when I click on the run button in simulation, it shows my estimated completion time. However, it takes much longer than that and yet the simulation doesn’t get completed (doesn’t complete 1000 in meantime).
Till you answer this, I will try running my simulation till 5000 iterations and see how long it takes to converge
Thanks!!
@MihirRayganga
First off, there are many reasons why a simulation doesnt converge. Some of it has to do with the settings in the Numerics section.
- what solvers you use
- what schemes you use
- residual controls
and so on…
However, I know from experience that a bad mesh / bad geometry does effect meshing and simulation times. when you have large amounts of illegal cells then it takes the mesh more time and effort to be created which then causes the simulation to take longer to solve.
To fix illegal cells, use the mesh quality feature to check for two important areas. Non-orthogonality and minimmum cell volume /ratio.
Improving your geometry will significantly speed up meshing/simulation times. you should be doing MULTIPLE iterations of meshing and geometry fixing before you even attempt a simulation
Dan